燃气轮机轮盘的机械加工中,轮槽加工难度最高、工作量最大,是技术关键所在。现阶段国内几大燃气轮机厂通过技术革新,引进大型复杂高精度轮槽拉床,对轮盘轮槽的加工由传统的专机铣削加工逐渐改为拉削工艺。大型燃气轮机机组的转子轮槽均为枞树型叶根轮槽,型线轮廓大,因此,需要的拉刀型线轮廓大(即轮槽拉刀的齿距大、齿槽加工深度较深),齿槽加工时切削量大,切削负荷大,刀具磨损快,且燃气轮机轮槽拉刀材料为高性能高速钢,强度高,切削性能差,因此其刀具结构复杂、加工难度大、效率低。
(一) 枞树型榫槽拉削的工艺特点
国内几大汽轮机厂均从国外进口大型复杂高精度轮槽拉床,同时进口大量燃气轮机轮盘枞树型轮槽加工用精密组合式拉刀。国外也仅有欧洲、日本等少数几大工具制造商能够制造此类拉刀,如德国HOFFMANN、法国SMOC、日本NACHI。下图是涡轮盘的枞树型榫槽。
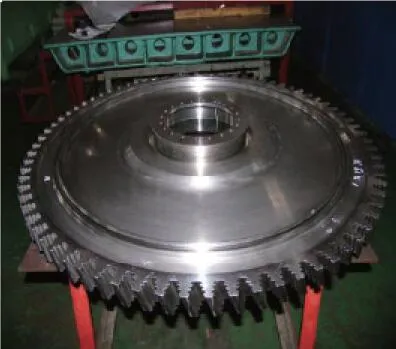
涡轮盘的枞树型榫槽
加工燃机轮盘叶根槽的拉刀属外拉刀,由多组拉刀组成,如最长的是F级燃气轮机第三级轮盘拉刀,长达21m,分为7组,每组长为3m,由6段500mm长的拉刀组成。某燃气轮机叶轮枞树型榫槽的形状是一条连续分布的曲线,榫齿齿顶和齿底均为圆弧。枞树型榫槽拉削选用粗拉刀和精拉刀组成的成套拉刀分别完成粗加工和精加工。其拉削形式分为非型线部分和型线部分。成套拉刀实现拉削过程如图所示,通过粗拉削和精拉削共12道工序实现榫槽的型线加工。
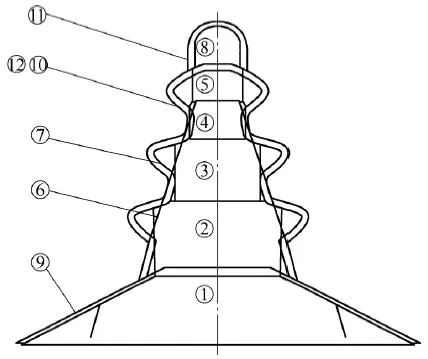
成套拉刀实现拉削过程示意图
(二)枞树型榫槽拉刀选用的注意事项
燃气轮机轮盘枞树型榫槽加工用精密组合式轮槽拉刀,以下简称拉刀。
(1)拉刀采用高性能高速钢材料,通过合金元素的配比并采用独特的热处理工艺,改善产品的硬度、强度、热硬性、韧性及耐磨性,提高产品使用寿命。选取拉刀材质需要综合考虑轮盘材质的加工性能、轮盘精度要求、刀具成本和拉刀刃磨等因素,建议可以选用钼-钴和钨-钴类超硬高速钢材料,如W2Mo9CrVCo8。硬质合金刀片在硬度、耐磨性和切削用量等方面强于高速钢,但是硬质合金刀片不能承受较大的冲击力,强度是高速钢的三分之一,且热处理困难。K类硬质合金韧性好、导热性好,可进行粗加工,M类硬质合金适用于精加工,但刀具寿命较低。
(2)燃气轮机轮盘枞树型榫槽加工用精密组合式拉刀,由粗拉刀、半精拉刀、精拉刀、修整拉刀精密组合而成,包括粗拉轮槽深拉刀、粗拉轮槽齿形宽拉刀、半精拉轮槽轮廓拉刀、精拉轮槽顶面拉刀、精拉刀轮槽底面拉刀、精拉轮槽轮廓拉刀以及修整轮槽轮廓拉刀等。对高温合金材料的榫槽拉削时采用高速钢的拉刀,粗拉刀的后角为5°~6°,精拉刀后角为4°~5°;采用粉末高速钢的拉刀,其前角为5°~8°,后角为4°~5°。
(3)粗拉刀组中的粗拉轮槽深拉刀和粗拉轮槽宽拉刀采用分体式结构,拉刀齿部分选用高性能高速钢,刀体选用优质工具钢,节约了30%拉刀原材料成本,大大提高了拉刀性价比。
(4)精拉轮槽轮廓拉刀采用同廓式轮切结构,实现枞树型榫槽的同廓成形加工,减小了轮槽拉刀切削力,提高了加工件齿面精度,保证枞树型榫槽齿形轮廓度误差值<0.01mm,同时保证枞树型榫槽齿形工作面齿距误差在0.005mm内。
(5)拉刀齿槽分层多刀粗精铣和齿形数控磨削加工工艺技术,设计相配套的拉刀铣齿槽和数控磨削装置等先进专用工装夹具,应用于燃气轮机轮盘枞树型榫槽加工用精密组合式拉刀的整个生产全过程中,增大了刀具加工系统的刚度,提高刀具的加工精度。型线是否合格主要影响的因素有:轮盘材质的热变形或轮盘材质的弹性变形。一般来说,拉削速度为1~2m/min,粗拉刀的齿升量一般为0.05mm,而精拉刀的齿升量为0.01~0.02mm。