HSK工具系统的选用
时间:2024-04-09 16:14:05 来源:admin 点击:0次
在高速切削加工中,根据加工要求正确、合理地选用HSK刀柄十分重要。在选择HSK刀柄的型号和规格时,主要的考虑因素包括:主轴的最高转速、刀柄的结构特点和承载能力、刀具及配套件的普及程度等。
A型有传动槽,相对来说A型传递扭矩较大,可进行一些重切削。A型刀柄除有传动槽之外,还有手动固定孔、方向槽等,则比较来说平衡性较差。所以转速就相对较低,可在主轴转速为20000~30000r/min的机床上使用。E型没有传动槽,传动的扭矩就比较小,只能进行一些轻切削。而且也没有手动固定孔、方向槽等,属于固有对称型,所以E型更适合于高速加工。F型和E型的区别在于:同样标号的F型和E型刀柄(比如F63和E63),F型刀柄的锥部要小一号。也就是说F63和E63的法兰直径都是φ63mm,但F63的锥部尺寸只和E50的尺寸一样。所以F63和E63相比,其主轴轴承小,转速要更快些。HSK工具系统的6种规格及其应用领域如表所示。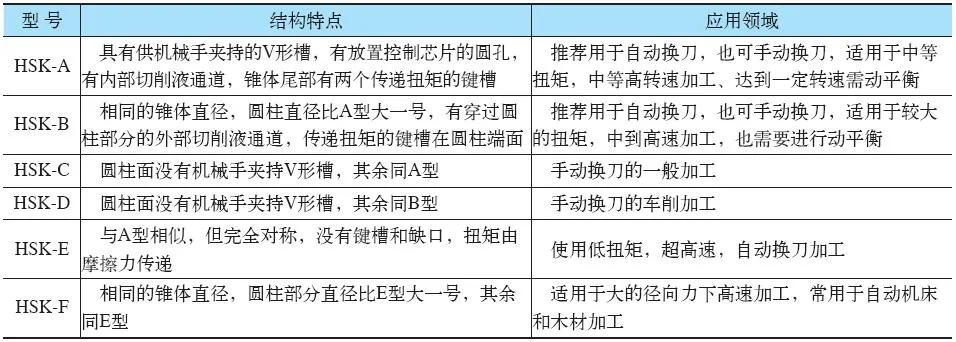
(1)刀柄型号的选择。由HSK刀柄的结构特点可知,A、B型刀柄主要用于带有自动换刀装置机床的中高速加工;C、D型刀柄主要用于采用手动换刀的中高速加工;而E、F型刀柄由于无任何槽和切口的对称结构,动平衡性较好,因此适用于超高速加工。国内采用DIN6989b-1中的A型和C型标准,如HSK50A、HSK63A、HSK100A等。HSK50和HSK63刀柄的主轴转速可达25000r/min,HSK100刀柄可12000r/min,精密平衡后的HSK刀柄可达40000r/min。随着转速增加,径向刚度将有所降低。下图为HSK与BT锥柄主轴转速与径向刚度关系的比较。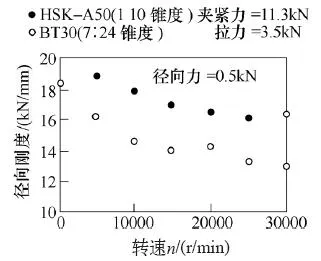
(2)刀柄规格的选择。选择HSK刀柄规格时,主要应考虑刀柄的承载能力(包括极限弯矩和极限扭矩),应根据实际加工时切削力产生的弯矩和扭矩,而承载弯矩的能力与夹紧力有关,实际上刀柄上承受的弯矩是由横向作用在刀具上的力产生的。刀柄的弯矩承载能力是在弯矩作用下,使刀柄法兰接触面的一边开始分离时的弯矩值,从这个临界弯矩值开始,弯矩-变形特征曲线的走向明显变陡,表明刀柄装夹的连接强度迅速降低。在接近临界点时,连接强度已经不够,尽管此时刀柄的法兰面与主轴端面还保持全面接触,但弯矩已接近使两者分离的临界值。这个临界弯矩的大小主要取决于拉紧力,因此加大拉紧力可以提高最大弯矩。这一点对悬伸较长的刀具有特殊的意义,此时一个较小的切削力就会产生较大的弯矩。但是加大拉紧力会增加作用在刀柄夹紧斜面上的总载荷,尤其是在高使用转速下,由于离心力的作用,内部夹爪所施加的夹紧力随之增加,致使夹紧的可靠性得以提高,但另一方面却使刀柄最薄的部位承受很大的载荷,导致刀柄损坏。损坏扭矩的大小与材料密切相关。如能正确选用材料,则可明显提高刀柄的承载能力。为了确定刀柄的最大扭矩承载能力,仅做静态试验还不够,在切削加工中所产生的动态激振的持续作用下,刀柄承受扭矩的能力明显下降。对于所有的材料动态承载能力大的只有静态试验时的7%。下面仅以HSK-63型刀柄为例对各种规格的HSK刀柄进行比较。1)HSK-63A-C型刀柄夹紧力:15kN,18kN,21kN。2)法兰端面分离弯矩:420Nm,460Nm,510Nm。3)滑动扭矩:115~155Nm,138~186Nm,161~218Nm。4)静态试验破坏扭矩:2200Nm(16MnCr5,56HRC),2400Nm(41Cr4,53HRC),3300Nm(X46Cr13,53HRC)。5)动态试验破坏扭矩:1600Nm(16MnCr5,56HRC),1800Nm(41Cr4,53HRC),2400Nm(X46Cr13,53HRC)。6)最高使用转速:22500r/min(最小过盈配合),27500r/min(最大过盈配合)。对于E型结构(不带键槽)的HSK刀柄,可传递的最大扭矩是靠刀柄与主轴之间的摩擦实现的,其大小除与锥度配合精度之差有关外,还取决于拉紧力。一个HSK63号刀柄的滑动扭矩在按照DIN标准推荐的18KN拉紧力情况下为138~186Nm,如果把拉紧力提高到21kN,滑动扭矩大约可提高20%,达161~218Nm。具体选择时可查阅相关手册,根据其所列的极限弯矩和极限扭矩来选择刀柄规格。下表为HSK刀柄的规格分布。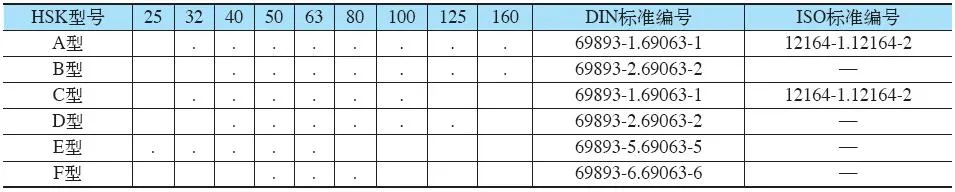
目前使用最广泛的是HSK-A型,大约占总量的98%,HSK-A型刀柄如图所示。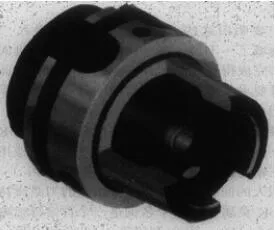